Properties
Our workpiece positioners represent the highest-in-class technology which is not manufactured elsewhere. Their numerous smart functionalities ensure running the production efficiently, processing workpieces in a manner as straightforward as possible and reaching high-quality output time and again. The properties for moving workpieces and adjusting movement speed increase worker safety and prevent machine breakdowns by eliminating collisions. We also provide portable and mobile workpiece positioners!
- The cylinders’ measurement rods or laser sensors ensure that both ends of the workpiece are moved simultaneously.
- Proportional valves ensure controlled accelerations and lifts while preventing swings.
- Frequency converters adjust speed, ensuring that rotational movements start and end smoothly. When the workpiece is already moving, the speed can be adjusted in stages.
- Collision thresholds can be saved for various heights so that the workpiece and positioner can move freely without any risk of collision.
- The option to program work cycles and save work stages enables completing the work stages more quickly while ensuring consistent quality.
- The workpiece positioner always turns the object to the correct angle automatically.
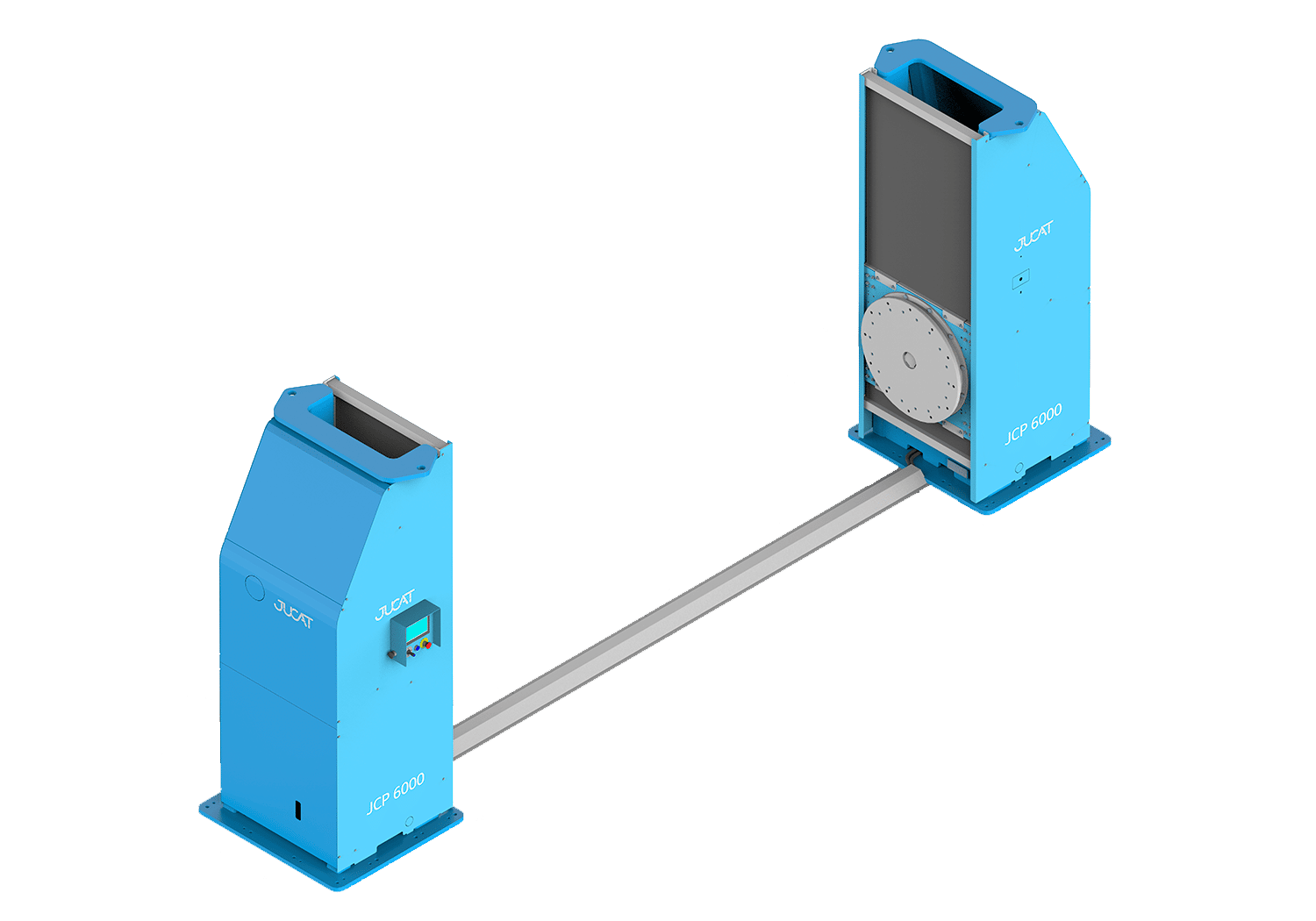
JCP
Single-axle workpiece positioner
Grill-type positioner that rotates the workpiece around a single axle. The workpiece is attached to plates in the positioner’s opposite poles, after which both ends of the workpiece can be lifted, lowered and rotated simultaneously. The JCP positioner is used particularly for handling large, heavy and elongated pieces such as frames. There is no limit to the length of the workpiece. The positioner can be used for handling pieces of any length.
JCP workpiece positioners | JCP 1500 | JCP 3000 | JCP 6000 | JCP 12000 | JCP 16000 | JCP 32000 |
---|---|---|---|---|---|---|
Lifting capacity | 1500 kg/pair | 3000 kg/pair | 6000 kg/pair | 12000 kg/pair | 16000 kg/pair | 32000 kg/pair |
Rotational torque | 2500 Nm | 6000 Nm | 8000 Nm | 10000 Nm | 10000 Nm | 18000 Nm |
Tilt torque | 3000 Nm | 7500 Nm | 7500 Nm | 12000 Nm | 20000 Nm | 50000 Nm |
Lifting range | 700-1800 mm | 700-1800 mm | 800-2000 mm | 800-2000 mm | 800-2000mm | 1000-1800 mm |
Plate diameter | 500 mm | 750 mm | 750 mm | 950 mm | 950 mm | 1490 mm |
Weight/unit | 800 kg | 1000 kg | 1000 kg | 1250 kg | 1300 kg | 4800 kg |
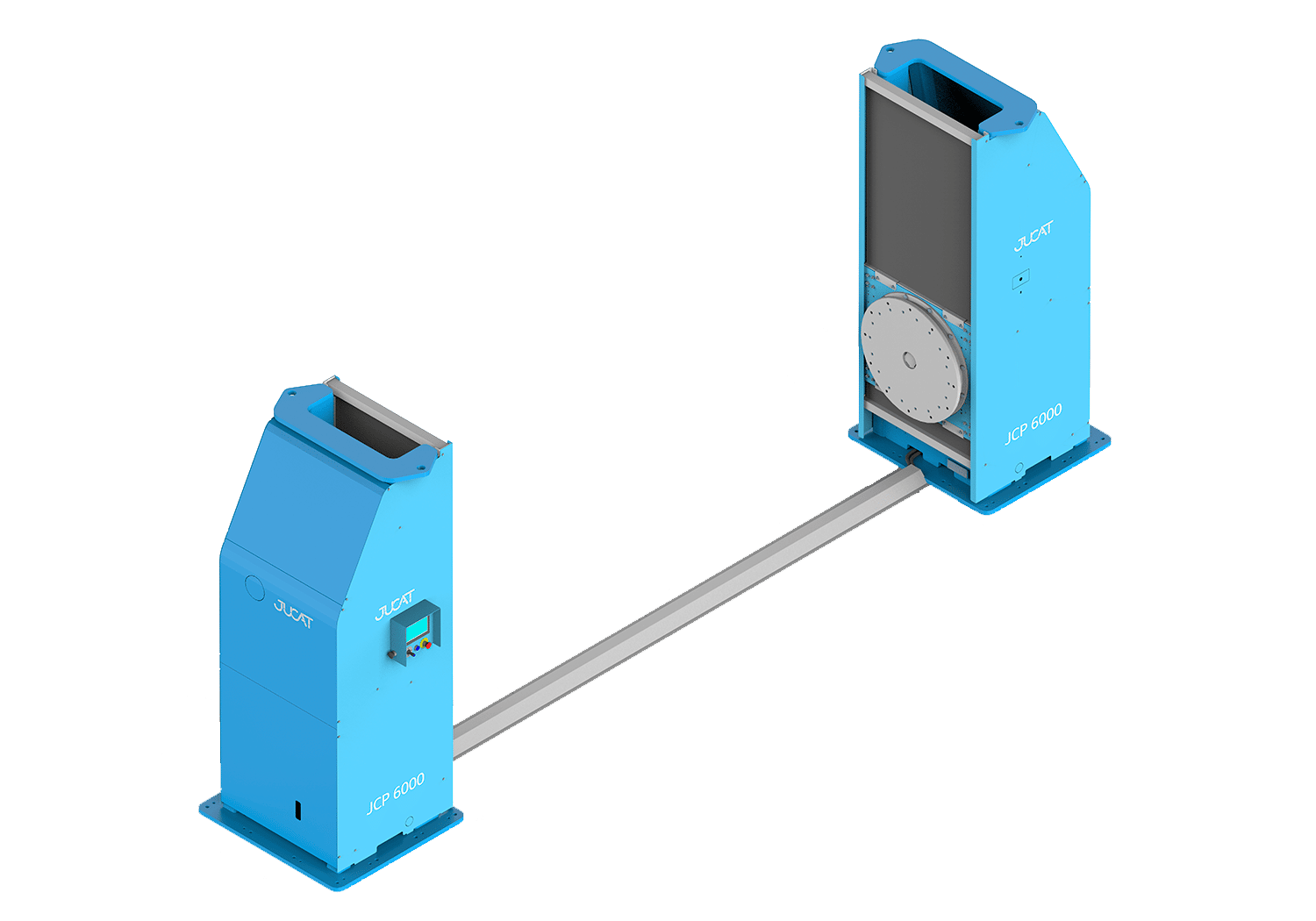
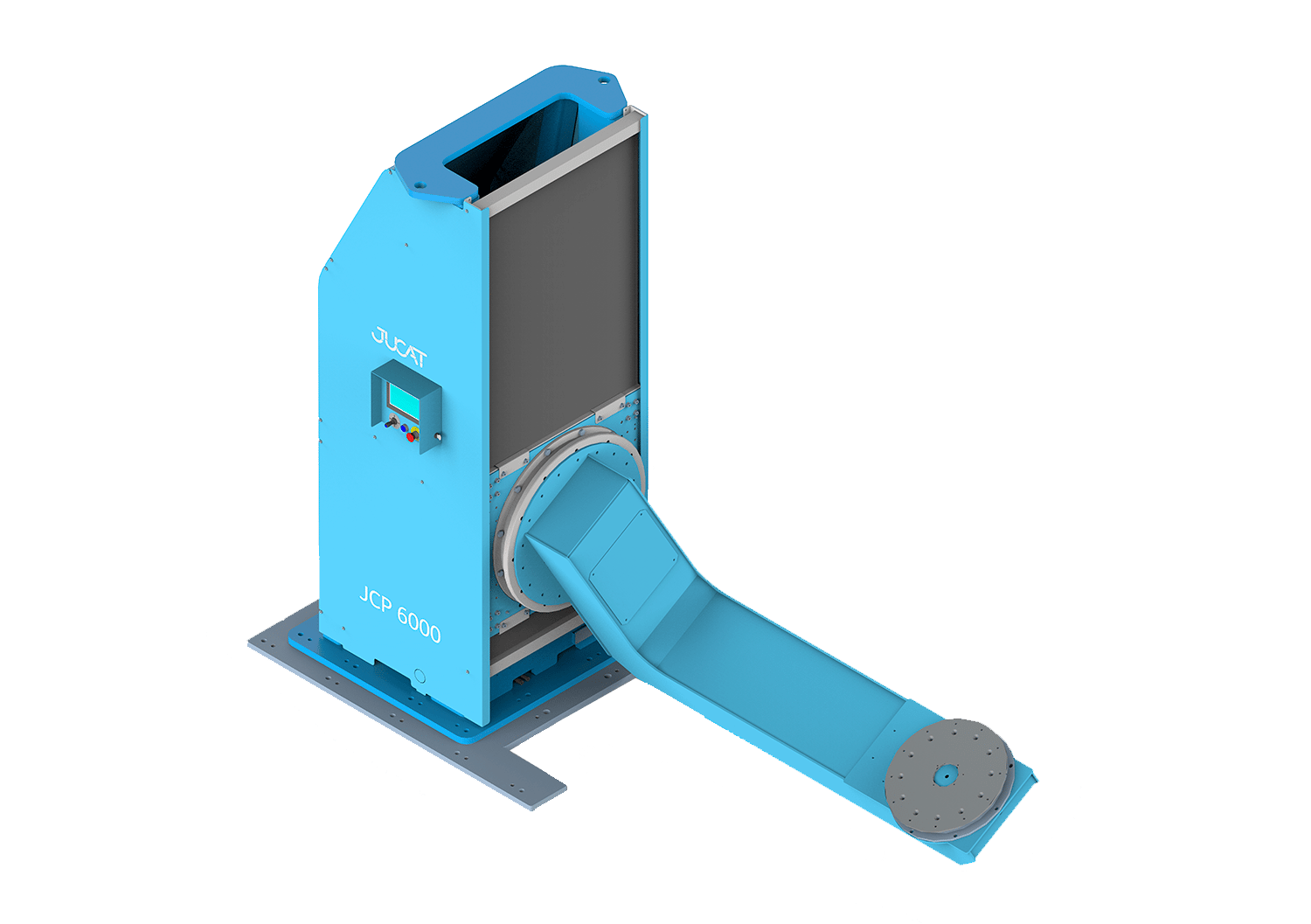
JCL
Double-axle workpiece positioner
The L-shaped positioner enables rotating the workpiece around two axles upward, downward and sideways up to 360 degrees. This allows placing the workpiece precisely to the desired position. The JCL workpiece positioner can be used for handling medium-size products with a maximum diameter of 3 metres.
JCL workpiece positioners | JCL 750 | JCL 1500 | JCL 3000 | JCL 8000 |
---|---|---|---|---|
Lifting capacity | 750 kg | 1500 kg | 3000 kg | 8000 kg |
Rotational torque | 2500 Nm | 2500 Nm | 6000 Nm | 10000 Nm |
Inclination torque | 2500 Nm | 6000 Nm | 10000 Nm | 18000 Nm |
Rotation diameter | 1500 mm | 3000 mm | 3000 mm | 3600 mm |
Tilt axis height | 700-1800 mm | 900-1900 mm | 1000-1800 mm | 1000-1800 mm |
Offset between tilt axis and plate | 350 mm | 500 mm | 500 mm | 500 mm |
Plate diameter | 500 mm | 500 mm | 750 mm | 950 mm |
Weight/unit | 830 kg | 1400 kg | 2000 kg | 6800 kg |
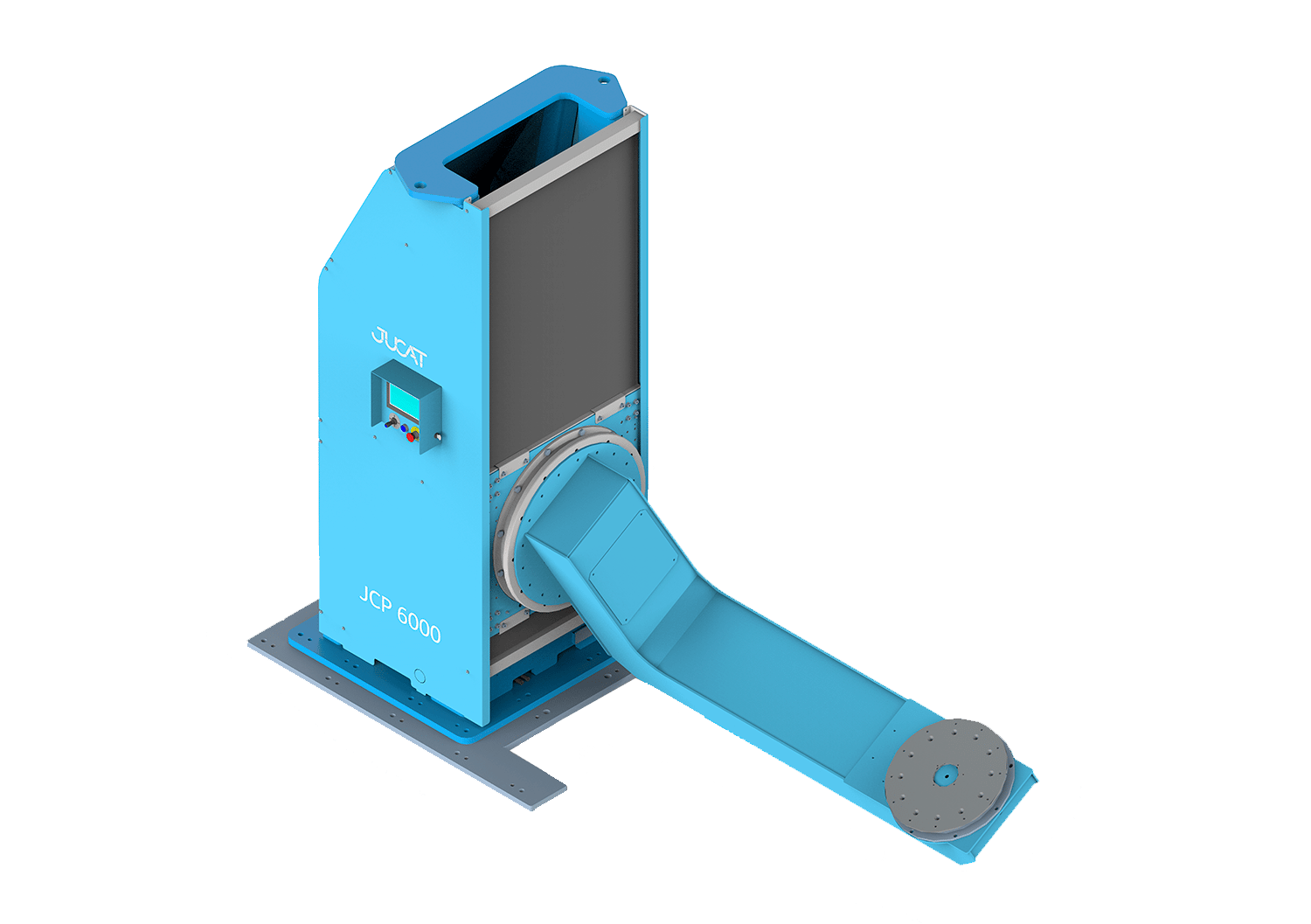
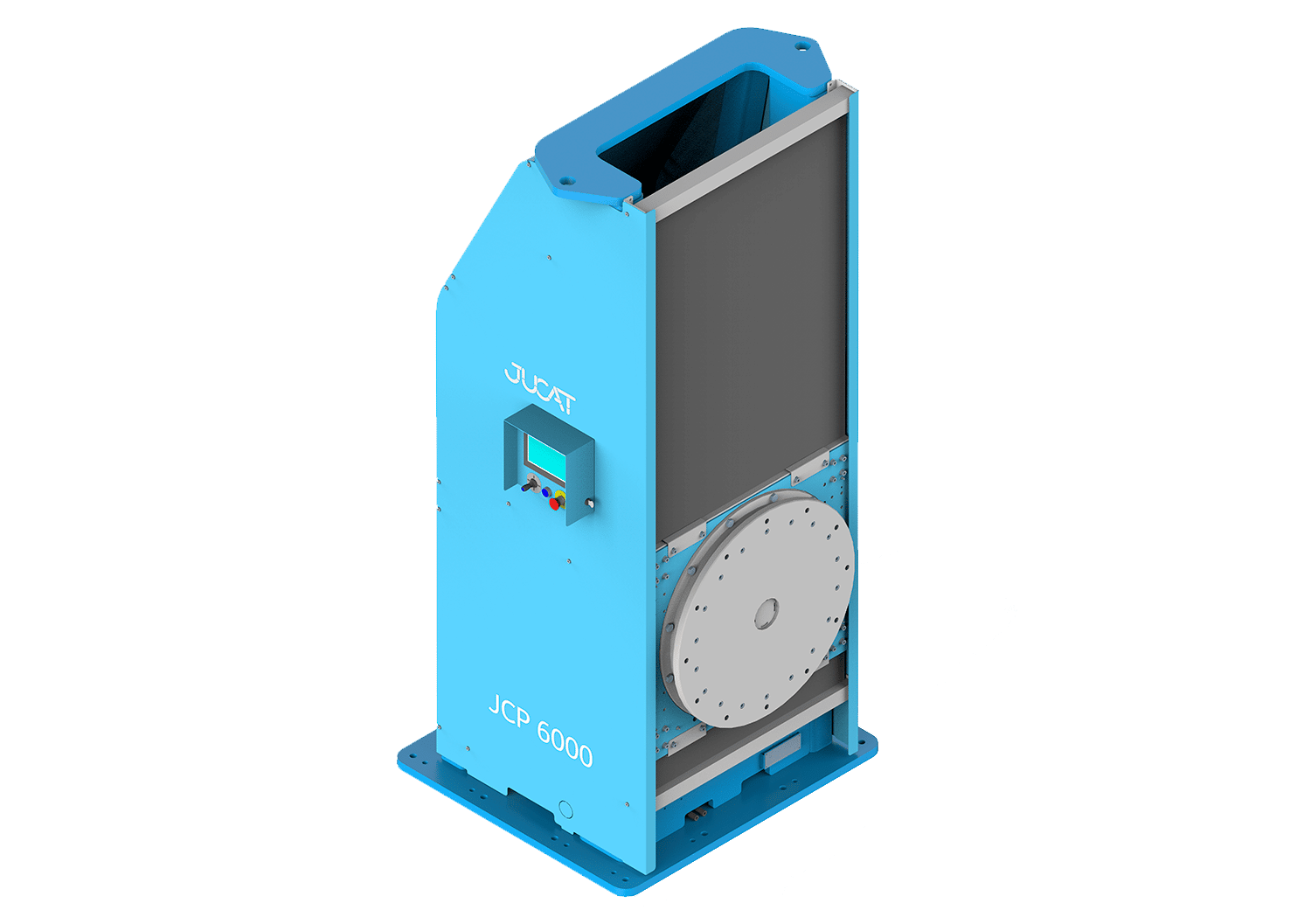
JCK workpiece positioners | JCK 750 | JCK 1500 | JCK 3000 | JCK 6000 | JCK 16000 |
---|---|---|---|---|---|
Lifting capacity | 750 kg | 1500 kg | 3000 kg | 6000 kg | 16000 kg |
Rotational torque | 2500 Nm | 6000 Nm | 8000 Nm | 10000 Nm | 18000 Nm |
Tilt torque | 3000 Nm | 7500 Nm | 7500 Nm | 12000 Nm | 50000 Nm |
Lifting range | 700-1800 mm | 700-1800 mm | 800-2000 mm | 800-2000 mm | 1000-1800 mm |
Plate diameter | 500 mm | 750 mm | 750 mm | 950 mm | 1490 mm |
Weight/unit | 785 kg | 875 kg | 1000 kg | 1250 kg | 4800 kg |
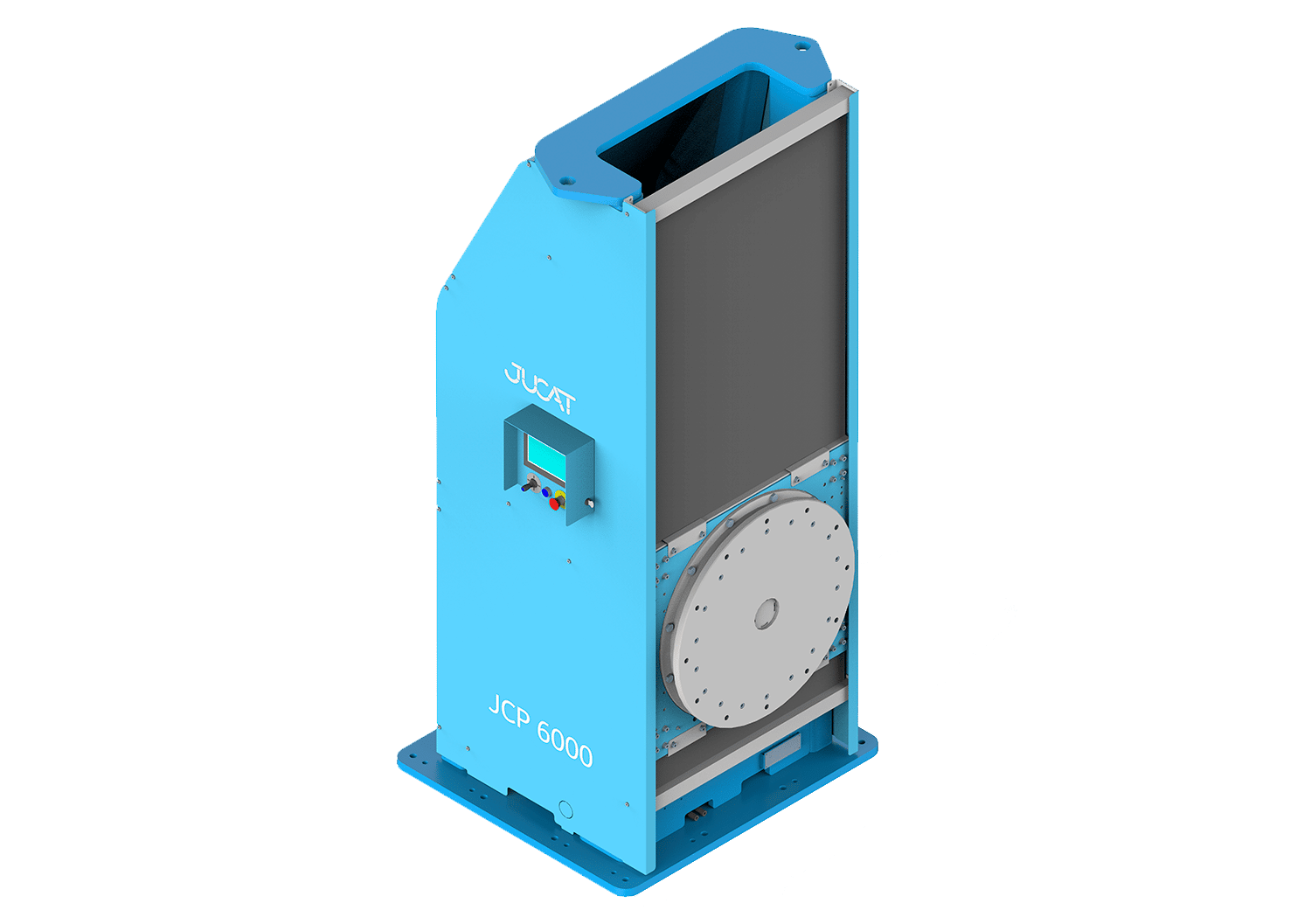
“It is easier for the welder to turn the product safely and without waiting for the crane. This speeds up the turnaround time for us. In the past, waiting for a bridge crane could take several hours for a single product, because the products we weld, which are now processed on Jucat’s welding positioner, involve a lot of turning. We have also received positive feedback from our employees about the ergonomics of getting the piece in the right working position every time,” says Rostedt.
Customised workpiece positioners to meet individual needs
In addition to the standard equipment range, we manufacture solutions designed to meet individual needs. As our advanced and effective design and production process enables us to provide our clients with all the benefits of high-grade technology, our products come with a productivity guarantee. Tell us what you require, and we can jointly design the optimal solution to meet your production needs!
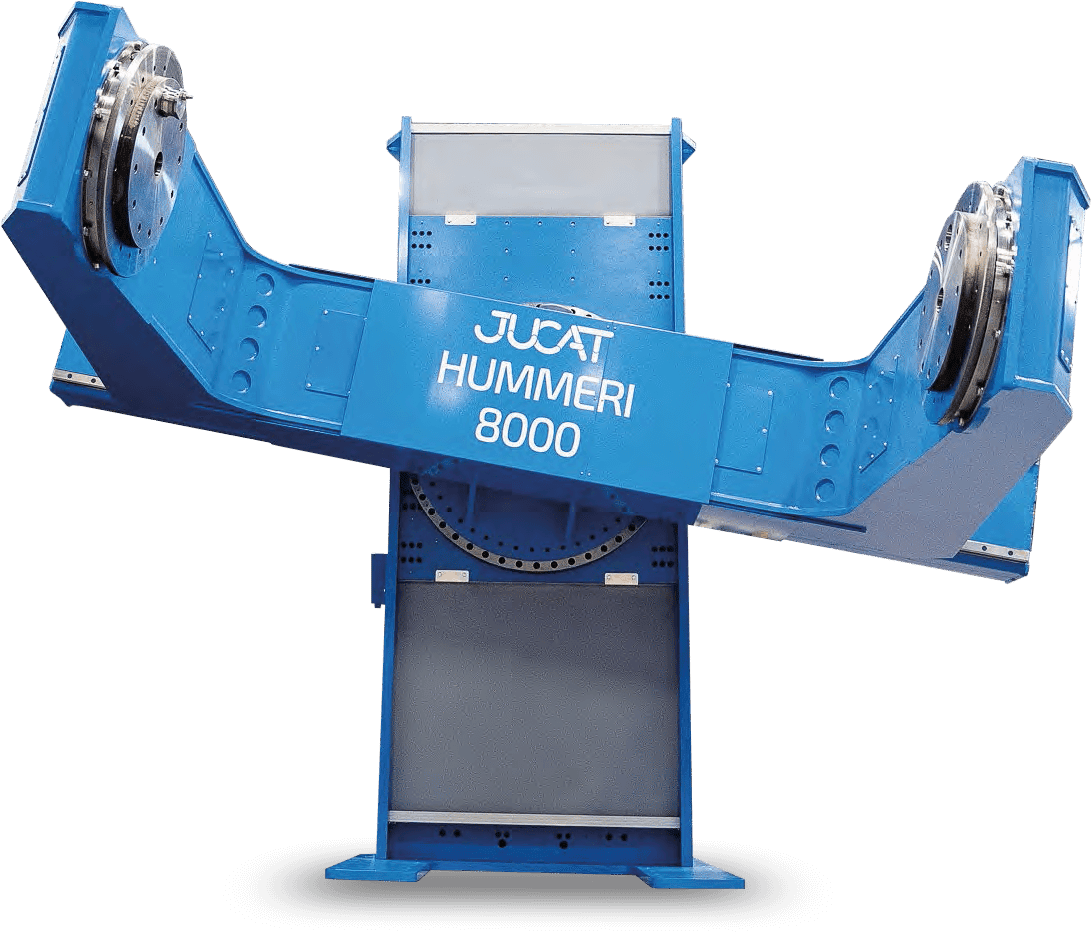
Hire a workpiece positioner to easily test it before investing
A workpiece positioner is an investment that quickly pays off through improved production efficiency. We offer the option to test a positioner easily by hiring it. The workpiece positioners available for hire are suited to handling light and medium-weight objects. Hiring the equipment quickly pays itself back with interest, and the hiring costs can be included directly in project sales. All you have to do is use the equipment – we take care of the rest.
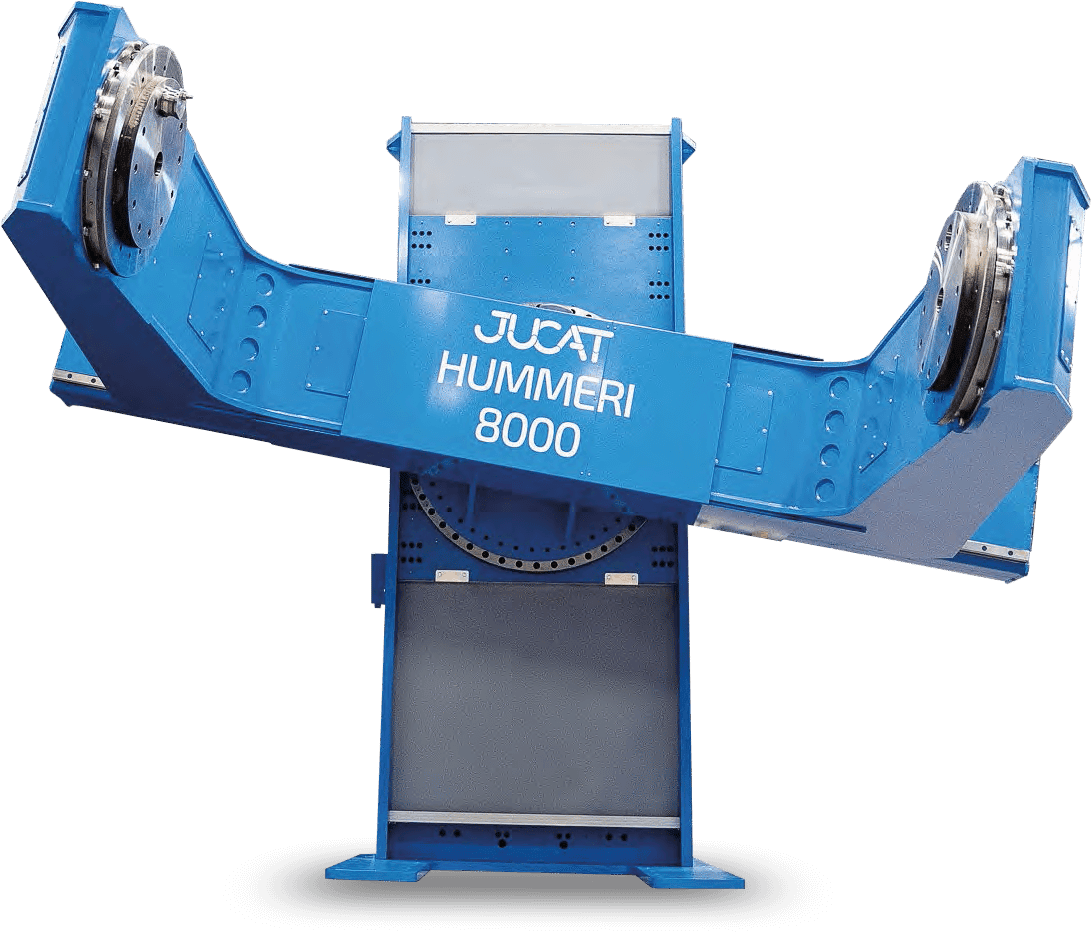
Get familiar with our content
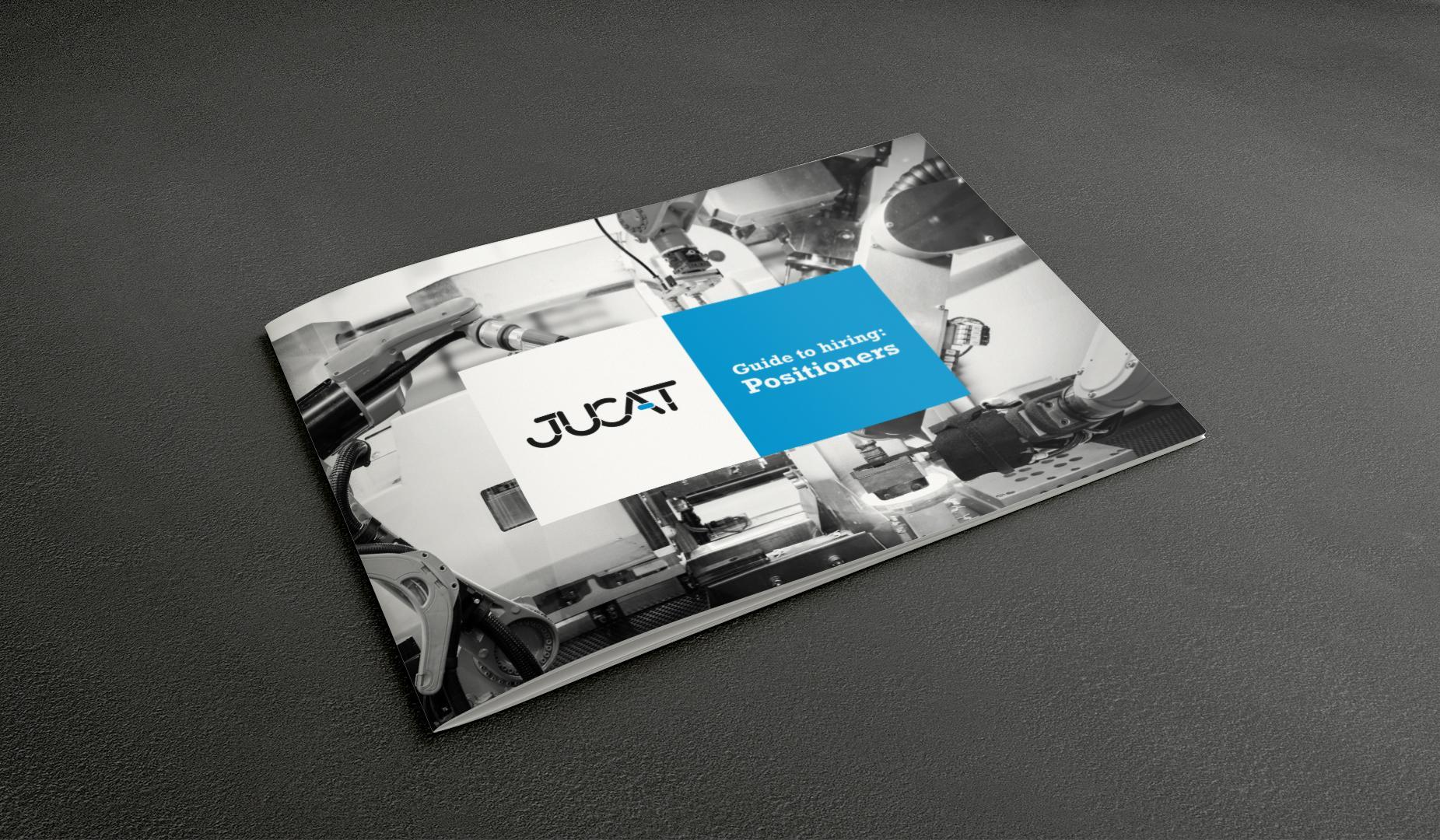
Guide to hiring:
Positioners
What you need to know about hiring our positioners?
In order to stay competitive, companies must increase production efficiency. This can be achieved quickly, without the need for heavy investment, by hiring a positioner. Our innovative positioners are developed to increase our customers’ competitiveness; they are a cost-effective option that boost the efficacy of industrial production in a number of ways. We compiled a comprehensive guide to the benefits of our positioners and our hiring service.